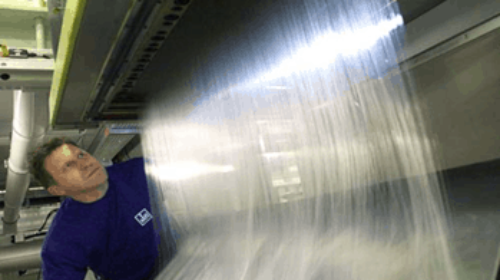
A polymer nonwoven fiber manufacturer significantly increased production capacity
THE SITUATION
Located in Tianjin, China, RENYI Industrial Co., Ltd specializes in polymer nonwoven fibers utilized in the production of masks. The company produces complex, high quality masks out of polypropylene.
Being a manufacturer of healthcare products, the company was being asked to flex their muscles and ramp up production in order to meet the rising demands to combat the COVID-19 outbreak. Die/spinneret and conveyor belt cleaning had always been an integral part of the production process, but they needed to achieve greater output of nonwoven fibers for face masks to meet the sudden surge in demand.
THE PROBLEM
As any polymer nonwoven fiber manufacturer knows, keeping the die/spinneret clean is a critical path to manufacturing a quality mesh for mask production. Yet, RENYI’s cleaning process was slow, tedious, and involved manual cleaning. They needed to ramp up production to meet market demands, but their current cleaning methods were too time consuming and caused extended downtime.
The excessive downtime was becoming unacceptable and causing a major production capacity issue. They were essentially losing one day per week just to clean the die. The die had to be baked in an oven for 4-6 hours, cooled for several more hours, power washed, baked in an oven again to dry, cooled again, and then workers had to manually drill out residual polymers left in the die holes.
Overall, the cleaning process for the 600mm dies was taking 20-24 hours.
THE SOLUTION
Cold Jets i3 MicroClean delivered MicroParticle dry ice media to clean their production equipment. The dry ice cleaning process was significantly faster and did not damage (mechanically or thermally) the dies.
The combination of dry ice blasting’s kinetic energy and thermal effects breaks the connection between the polymer and the die.
The dry ice blasting process brings a variety of advantages over traditional cleaning methods.
The process is non-abrasive and extends the asset life of the die. With dry ice, there is no longer a need to manually drill out die holes or scrape off excess polymer. Dry ice blasting is a dry process and does not require water or ultrasonic tank cleaning and does not produce secondary waste. It is also environmentally friendly and eliminates the use of chemicals.
THE RESULTS
With dry ice blasting, the polypropylene polymer was quickly and effectively removed from the die and conveyor belts. Cleaning time went from 20 – 24 hours to just 12 to 20 minutes. Since implementing Cold Jet dry ice blasting, RENYI Industrial’s productivity dramatically improved, recapturing one full day of production per week.
The dry ice cleaning process is a proven way to help polymer nonwoven fiber manufacturers become more competitive and meet the global market product demands.