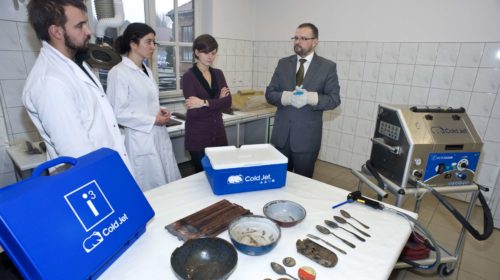
Offshore oil platform removes surface corrosion and failed coating
THE SITUATION
Corrosion is a major problem on offshore oil platforms. The pipework, machinery and the structure itself are exposed to extreme environments and the constant presence of aggressively corrosive elements. The areas vulnerable to corrosion require continual preventative maintenance to ensure a safe and prolonged operation. If corrosion is not handled appropriately, there is a potential for unsafe work conditions and even vital equipment failure, which would cause the platform operations to lose time and money as they await repairs. On most platforms, the pipework and machinery are covered in a protective coating, but even this will not fully protect the underlying surface, as the coating will begin to fail over time.
On an oil platform in the North Sea, the fabric maintenance team – who is responsible for maintaining the integrity of the platform – was working to remove corrosion and failed coating from gas lines within the gas compression module of the platform and re-coat them. The gas lines had exceeded the fabric maintenance strategy intervention levels and were beginning to show areas of material loss. The work would have traditionally required a shutdown period and had been outstanding since 2010. The scope of work had been deferred from previous shutdown periods due to the potential of grit ingress damaging open, sensitive and rotating equipment within the module.
THE PROBLEM
When using traditional media blasting methods, full encapsulation is often needed as debris from blasting can become clogged in air intakes and potentially cause damage to rotating equipment, especially around sensitive areas, such as the gas compression module. For certain complex areas, the time and labor cost involved in erecting and dismantling traditional scaffolding and encapsulation can outweigh the rest of the project cost by a significant margin.
Traditional media blasting techniques, such as media blasting and high pressure water systems, present several other disadvantages that add costs and time to the project. These methods create hazardous waste and dust that is unsafe to breathe and has to be gathered and removed upon project completion. They also are typically only able to be performed during shutdown periods. The blast media and the secondary waste can damage mechanical and electrical equipment so this machinery must be shut down prior to the blasting. The overall process required when using traditional media blasting methods is more time and labor consuming. Encapsulation must be planned, assembled and then disassembled, blast media and the secondary waste must be gathered and disposed of and, once blasting is complete, the area must be given time to dry before re-coating. These methods can also be abrasive and reduce metal wall thickness.
The fabric maintenance team began to review dry ice blasting as an alternative cleaning process and recent projects that have used the technology on other platforms. The results of those projects gave the team confidence that it would be a fit for their platform. The team contacted Dry Ice Global (DI Global), a company that specializes in the rental of high performance dry ice production and blasting equipment, and began to pilot the dry ice blasting.
THE SOLUTION
DI Global are pioneers in the use of high-performance, high intensity dry ice blasting for fabric maintenance in the offshore oil and gas industry. The DI Global System is a fully integrated, transportable product that makes dry ice production (with a built-in Cold Jet pelletizer) and high pressure blasting (with a specifically modified Cold Jet dry ice blaster) in remote locations for extended periods of time. The aggression level can range from gentle cleaning to more aggressive blasting for fabric maintenance applications.
DI Global exclusively utilizes Cold Jet’s dry ice cleaning and production systems. Cold Jet’s dry ice cleaning systems use non-abrasive media in the form of recycled CO2 pellets that will not damage surfaces or equipment. The combination of dry ice cleaning’s kinetic energy and thermal effect breaks the connection between the dirt and surface, lifting away contaminants. Unlike blasting with other media, dry ice cleaning does not leave any secondary waste, because the dry ice particles sublimate upon impact – converting from solid to gas. Dry ice cleaning is safe and non-toxic, does not create downstream contamination, and reduces or eliminates employee exposure to dangerous chemical cleaning agents.
Dry ice cleaning removes heavy corrosion and defective coatings from pipework and allows for minimal disassembly, no drying time, reduced encapsulation and waste disposal, which optimizes the overall project time. The technology can be used during live operations with no damage to electrical components or rotating machinery, is non-abrasive and does not impact a new profile to the substrate. Rather, it exposes the existing profile that is present beneath the coating. Using dry ice blasting also allows for the surfaces to be re-coated immediately, further improving productivity.
The specifically modified Cold Jet blasters used by DI Global are ATEX rated for Zone 1 applications (For more information on safety specs, please refer to the end of the case study).
THE RESULTS
The fabric maintenance team was happy with the results. Dry ice blasting removed the light external corrosion found on the pipework and did not generate the secondary waste issues traditionally seen with grit blasting in and around the gas compression module. The team saved 1,000 man hours, or 125 man days, from the shutdown schedule as the work could be performed during live operations.
Significant productivity gains and cost savings were realized due to the man hours saved on scaffold assembly, encapsulation, masking up, day-to-day clean-up, final clean-up, scaffold dismantling and removal of all sheeting protection.
Added benefits included productivity levels of 4 – 5m2 (43 – 53ft2) per hour and delivering a consistent anchor profile of 70 – 110 um with SA2.5 cleanliness. Salts and other soluble contaminants were also able to be removed with no need for a water wash.
On another similar project, dry ice blasting formed part of a fabric maintenance campaign used by the existing fabric maintenance contractor. This brought nearly 300% gains in productivity and a 65% cost reduction compared with traditional methods.
The DI Global system can easily be retrofitted for existing users, and can be deployed in both offshore and onshore environments. Site trials have shown a 90% reduction in waste when compared with traditional methods while maintaining similar trigger time productivity. This means that users can enjoy the time and cost savings by removing encapsulation and reducing clean up.